We use cookies to make your experience better. To comply with the new e-Privacy directive, we need to ask for your consent to set the cookies. Learn more.
Bredent Burs and Discs
Diatit Tungsten Carbide Burs
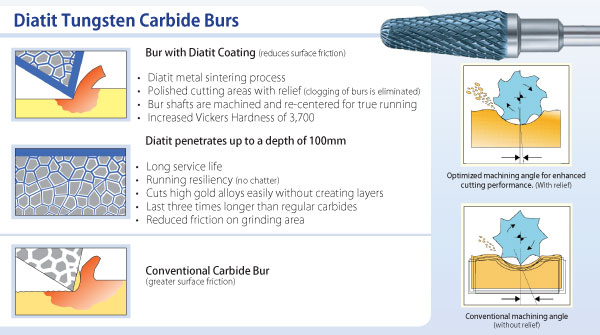
Diatit tools feature the advanced Diatit wear protection coating. This is a special material which is added into the surface of the bur after it has been produced. It hardens the tool surface and reduces the surface friction.
This comprehensive hardening process results in a tool which features very smooth rotation and precise cutting performance from the very beginning - and this is provided over a considerably long period. Accurate removal of material is ensured. Additionally, the service life of the tool (compared to uncoated carbide burs) is increased considerably by the hardening process.
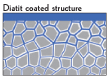
A small dimple is prepared with the Diatit Center Drill (#330 006 60) to determine the position of the drill hole. The dimple will center the drill and keep it in position.
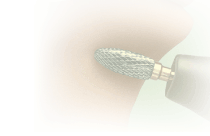
The hole is drilled with the 1.5mm Diatit Multidrill (#330 007 30). The dimple is used to guide the drill into position.
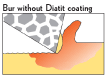
The waxing pins are inserted into the holes to check for proper positioning.
INSTRUCTIONS FOR USE DIATIT TUNGSTEN CARBIDE CUTTERS
Before using this product, please read and follow these instructions carefully.
1. Description of the Product
Cutters made of fine grain Tungsten carbides sintered onto a Tungsten carbide/cobalt base. Thanks for a special type of heat treatment (hot isostatic pressing), the sintered Tungsten carbide alloy is condensed again to reduce the remaining porosity immensely.
Diatit cutters are provided with a special anti-wear layer that, although it only adds 1 micron to the surface, penetrates up to 100 microns into the metal surface.
2. Advantages
Thanks to the Diatit anti-wear layer, these cutters exhibit an extremely high Vickers hardness value of 3700. Without this Diatit layer, they have a Vickers hardness of 1850.
This leads to:
" Exceptionally high structural strength and resulting sharp cutting edges over a long period of time, which will not disintegrate.
" Hardness values double those of cutters without an anti-wear layer.
" Three times the service life of cutters without an anti-wear layer.
" Grinding performance remains constant throughout a long period of time, which reduces costs and increases profit.
" The particles created during grinding cannot become attached to the finely honed; smooth coated cutting edges of the cutter
Whereas when using non-coated cutters, the particles may even become welded to the teeth of the cutter due to the heat and pressure involved.
If there are no particles on the cutting edges:
" The friction is reduced by half and less heat is generated.
" If the exterior shape of the cutting edge does not change, it cuts neatly and produces smoother surfaces.
" The cutter runs smoothly on the restoration.
" Less friction, reduced stress on the teeth of the cutter, which will not disintegrate.
Diabolo Sintered Diamonds
Friction Grip - Diabolo for all ceramic cores
Fast, efficient preparation of each type of Zirconia, Alumina Oxide and other hard tooth materials.
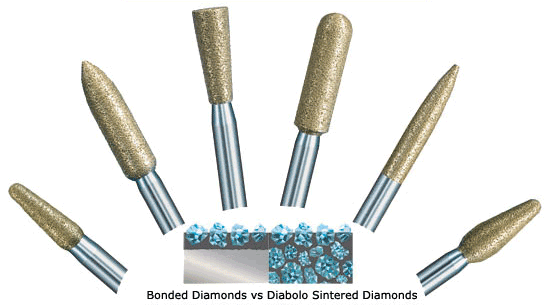
Carefully selected natural diamonds are entirely integrated into a mixture of metal and binding material. Due to the special manufacturing process, worn out diamond grit is automatically removed and replaced with new diamonds so that automatic sharpening is achieved. The auto sharpening effect enables it to perform highly difficult processing of dental material in a simple, fast, and efficient way.
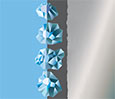
In the case of electro deposited grinding tools, the diamond crystals have been attached to the bur blank in a metal bond
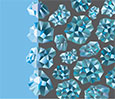
In the bredent sintering method, the razor sharp diamond crystals are embedded in an adapted mixture of binding material.
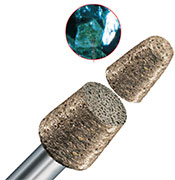
Giflex-TR Diamond Disc
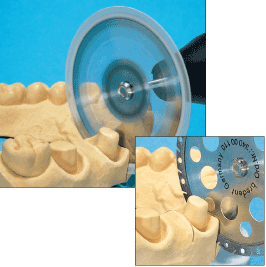
Giflex-TR is a disc for handpieces that features diamond-coating on both sides and is especially suitable for cutting dies out of plaster, refractory and resin. Calculated chip spaces in the area of the diamond coating ensure quick removal of the grinding dust and increase the cutting performance of the disc. Giflex-TR allows for quick, smooth, and reliable cutting even of very hard plaster and resin. Troublesome chattering and jamming of the disc is avoided.
Larger holes in the diamond free section reduce the friction heat. The disc will not overheat even if deep cuts are carried out. The running transparency allows for a better view into the saw cut.
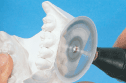
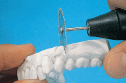
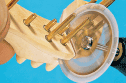
Transflex Diamond Discs
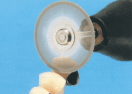
Diagonally arranged cutouts for running transparency with high breaking strength and optimal grinding capacity.
Transflex is well suited for dividing and separating in the areas of the anterior and posterior teeth and in the approximate shaping. The specially diagonally arranged cutouts ensure running transparency with high stability and abrasiveness of the grinding disc.
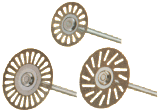
Diagonally arranged cutouts for running transparency with high breaking strength and optimal grinding capacity. These discs are designed for delicate work and have to be handled accordingly
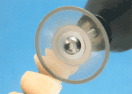
The highly flexible grinding wheel with transparency for safe, concerted grinding.
Transflex is well suited for dividing and separating in the areas of the anterior and posterior teeth and in the approximate shaping. The specially diagonally arranged cutouts ensure running transparency with high stability and abrasiveness of the grinding disc.
The highly flexible grinding wheel with transparency for safe, controlled grinding
Diacryl Diamond Instruments for Acrylic
Save time and improve quality by grinding acrylic with diamond coated Diacryl rotary instruments. Thanks to their uniform, coarse grit diamond particles with sharp edges and their specific shapes, Diacryl diamond instruments are excellent for trimming acrylic dentures quickly and accurately. Thanks to their extra coarse diamond grit and large diameter, these instruments grind aggressively and quietly.
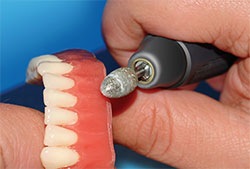
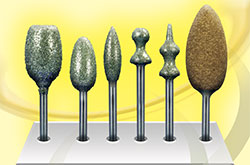
Diagen Turbo Grinders
Diamond instruments for metal, porcelain, zirconia and In-ceram
The diamond instrument with exceptional grinding performance thanks to the special Diagen diamond bonding. High grinding performance and abrasion on metal and porcelain surfaces - only minimal pressure has to be exerted. The prolonged service life in comparison to conventional bonding systems provides for a wide range of applications and high efficiency.
Maximum grinding power and abrasive capacity on metal and ceramic surfaces at reduced pressure. Increased surface life compared to conventional binding material allows for a wide range of applications and thus high efficiency.
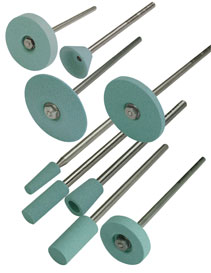
The diamond instrument with exceptional grinding performance thanks to the special Diagen diamond bonding. High grinding performance and abrasion on metal and porcelain surfaces - only minimal pressure has to be exerted. The prolonged service life in comparison to conventional bonding systems provides for a wide range of applications and high efficiency.
Maximum grinding power and abrasive capacity on metal and ceramic surfaces at reduced pressure. Increased surface life compared to conventional binding material allows for a wide range of applications and thus high efficiency.
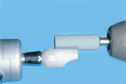
In the case of electro deposited grinding tools, the diamond crystals have been attached to the bur blank in a metal bond
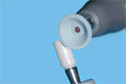
In the bredent sintering method, the razor sharp diamond crystals are embedded in an adapted mixture of binding material.
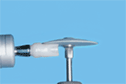
In the case of electro deposited grinding tools, the diamond crystals have been attached to the bur blank in a metal bond
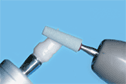
In the case of electro deposited grinding tools, the diamond crystals have been attached to the bur blank in a metal bond
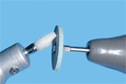
In the bredent sintering method, the razor sharp diamond crystals are embedded in an adapted mixture of binding material.
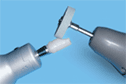
In the case of electro deposited grinding tools, the diamond crystals have been attached to the bur blank in a metal bond
Diatit MultiDrill System
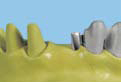
1. The patrix of the bridge sectioning attachment features the same direction of insertion as residual abutment teeth.
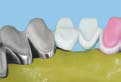
2. Wax-up the second bridge element, cast and finish.
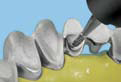
3. Prepare a small groove at the point where the screw is to be placed.
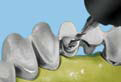
4. Drill through the secondary element approx. 1.5mm deep into the primary element using the Diatit-Multidrill.
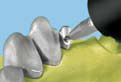
5. The patrix of the bridge sectioning attachment features the same direction of insertion as residual abutment teeth.
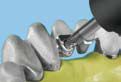
6. Assemble the primary and secondary element and drill up to the stop using the tungsten carbide facing cutter.
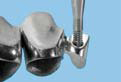
7. Cut the thread into the primary element. First use the first tap and then the last tap.
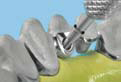
8. Assemble primary and secondary element and turn into the screw.
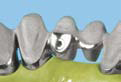
9. The screw head with the secondary element is ground flush and polished.
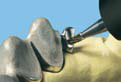
10. Grind a small groove into the patrix using the center drill.
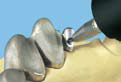
11. The Diatit-Multidrill drills down to the exact depth.
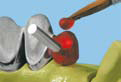
12. Integrate the auxiliary modeling element into the pattern using the brush resin.
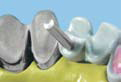
13. Complete the pattern using modeling wax.
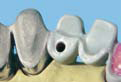
14. Turn the auxiliary modeling element with a pair of pliers and remove it.
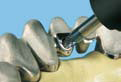
15. After casting, assemble the bridge elements. Drill to the stop using the facing cutter.
Tool Set M 1.4 / 1.6 Dimensions
Product | Item # | Ø | Length | Thread | Length/Head | Max. Reduction |
---|---|---|---|---|---|---|
Titanium screw M 1.4 |
330 007 00 | 2.1 mm | 4.5 mm | M 1.4/0.3 | 2.5 mm | 1.2 mm |
Titanium screw M 1.6 |
330 011 60 | 2.3 mm | 5.2 mm | M 1.6/0.35 | 2.5 mm | 1.2 mm |
Silicone Burs
The special cutting edge geometry allows the use of soft materials and transition zones towards hard resins. In orthodontics, silicone positioners can be perfectly ground due to the excellent guidance.
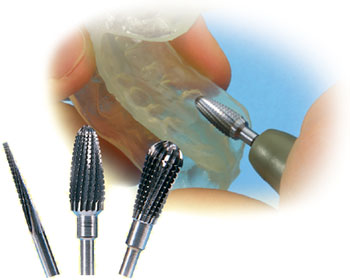
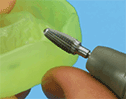
Thermoformed, soft thermoplastic plates with different degrees of hardness are rapidly and safely ground with these silicone burs; ideal for athletic mouth guards.
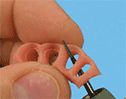
Due to the different shapes, these burs can be used to shape silicone in hardly accessible areas such as the alveoli of the gingival mask.
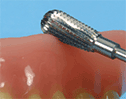
Due to the controlled removal of material, a smooth transition zone from the silicone to the denture resin is achieved. The ground surface is smooth and free from any residue.
Diamonds for Veneering Technique
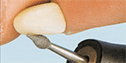
The concave part of this tool ensures perfect contouring of the approximal surfaces around the neck of the tooth. Enhanced aesthetics in less time.
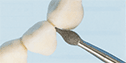
The very thin tip of this tool allows the efficient design of tooth necks for single crowns and bridges.
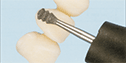
This tool can easily create uniform enamel bulges at the tooth neck. All tools can be used on ceramic and acrylic veneer materials.
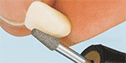
The conical grinding tool has a coated face which provides for universal application. The entire design process can be completed with this tool.
Milling Bur System
Overview
The Bredent Three Step Milling system consists of 3 burs of the identical shape, but each designed for different surface finishing. This will allow you to drastically cut finishing time by giving you the capability to precisely pre-mill in the wax stage. After casting, the metal milling bur is used to do the final finishing. This metal bur is exactly the same shape as the wax bur which minimizes the milling time required on the metal. The final high shine polish is achieved with the polishing bur. Using this system, you can save costs, time and material.
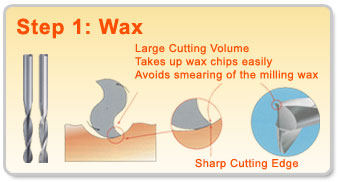

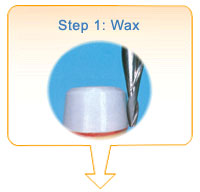
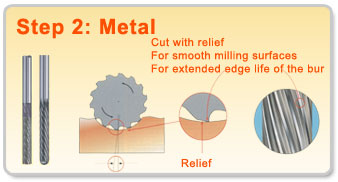

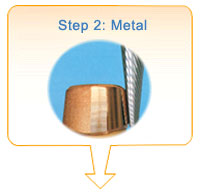
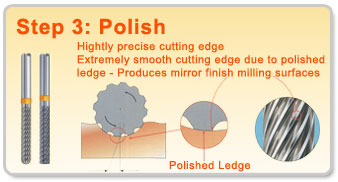
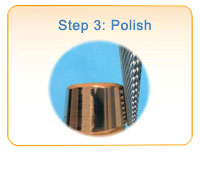
Groove Burs
The groove bur exclusively serves to prepare grooves. For this purpose the groove bur is only moved up and down in the vertical axis. The cut on the face simplifies extending the grooves to the cervical direction. At speeds of 15,000 - 20,000 rpm a fine cutting performance and a mirror-like high luster on the milling surface are obtained.
Shoulder Burs
The occlusal shoulder is prepared with a special shoulder bur. The shoulder bur features a face cut which smoothens the bottom of the shoulder. Optimum use of this tool is ensured at speeds of 15,000 - 20,000 rpm. A mirror-like luster on the milling surface is achieved with the relief cut. Additional polishing is not required.
Non-Precious and Titanium
A rich quantity of milling and drilling oil is applied onto the milling surface and a speed of 20,000 - 25,000 rotations per minute is used for milling. While adding a copious amount of milling and drilling oil, the milling surface is prepolished with the polishing bur at 20,000 rotations per minute and then polished to high luster at 10,000 rotations per minute.
The cutting edge geometry has been especially designed for rapid removal of material. The relief ensures smooth running and allows very smooth surfaces on the object to be milled. The wide relief extends the edge life and avoids breaking of the sharp cutting edges.
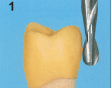
It is recommended to wax the entire crown in wax prior to starting the milling work.
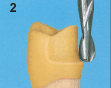
In the first step a shoulder with a margin step is prepared with a round 2.3mm parallel wax bur.
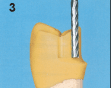
The insertion grooves are then prepared with the flat 1.0mm groove bur.
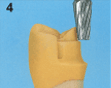
The final wax step is to mill an occlusal shoulder with the 2.7mm shoulder bur.
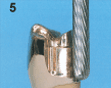
After casting the crown, the parallel surface is finished with the 2.3mm round metal bur.
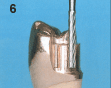
The insertion groove is finished with the same groove bur. The bur should only be moved up & down in the vertical axis.
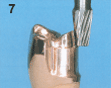
The occlusal shoulder is reworked with the 2.7mm shoulder bur.

Finally, a high luster is achieved on the parallel surface using the 2.3mm round polishing bur.
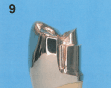
The bredent milling burs produce such a high shine that additional polishing is not needed..
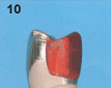
A secondary element with anatomy is created with the Pi-Ku-Plast pattern resin. (Pg. 115 and 116)
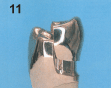
The secondary element is cast and fitted onto the crown.
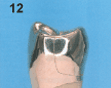
The low shrinkage of the Pi-Ku-Plast pattern ensures excellent precision of fit of the two pieces.