We use cookies to make your experience better. To comply with the new e-Privacy directive, we need to ask for your consent to set the cookies. Learn more.
BREDENT EQUIPMENT SUPPORT
Milling Machine BF-2
INSTRUCTIONS FOR USE MILLING TECHNIQUE
Before using this product, please read and follow these instructions carefully.
1. Indication Range:
The rotating tools for the milling technique are used in all fields of dental milling work.
2. Wax Burs
2.1 Modeling of the wax crown:
All types of modeling waxes that are suitable for crown and bridge techniques can be used for modeling.
2.2 Speed ranges:
Use the wax bur in a speed range of 3,000 - 5,000 rpm. Please exert only slight pressure during milling of wax.
2.3 Cleaning the wax bur:
The specially designed cutting geometry of the wax bur produces razor-sharp edges. Therefore, wax must never be removed with the fingers; this way injuries can be avoided. Remove wax residues with a brush, a soft cloth or with a steam unit.
3. Profiling Burs
3.1 Milling and drilling oil:
In order to achieve steadier running of the bur on the surface of the object, a smoother milling surface and extended service life, it is absolutely necessary to work with the Milling and Drilling Oil (Item # 550 000 08). Due to reduced evaporation, the oil produces a uniform lubricating film on the milling surface. It is recommended not to use ethereal oils.
3.2 Speed ranges:
Use the profiling bur at a speed range of 15,000 - 20,000 rpm. Please exert only slight pressure; this way the service life of the bur is considerably increased and a slight luster on the surface is obtained.
3.3 Cleaning the profile bur:
Clean the profiling bur with a soft cloth or with a steam unit.
4. Polishing Burs
4.1 Milling and drilling oil:
In order to achieve steadier running of the bur on the surface of the object, a smoother milling surface and extended service life, it is absolutely necessary to work with the Milling and Drilling Oil (Item # 550 000 08). Due to reduced evaporation, the oil produces a uniform lubricating film on the milling surface. It is recommended not to use ethereal oils.
4.2 Speed ranges:
Use the profiling bur at a speed range of 20,000 rpm. Please exert only slight pressure; this way the service life of the bur is considerably increased and brilliant surfaces on all precious metal alloys will be achieved.
4.3 Cleaning the polishing bur:
Clean the polishing bur with a soft cloth or with a steam unit.
5. Safety Recommendations
5.1 Safety clothing:
While working with the tools for the milling technique, safety glasses and standard safety clothing must be worn.
5.2 Damaged and twisted tools must be exchanged immediately since they affect the quality of the finished product. Damaged instruments increase the risk of serious injury.
6. Further Information
The information contained in this product information is always updated according to the latest knowledge and experience.
Therefore, we recommend that you read this information again before using a new package
Silano Pen
INSTRUCTIONS FOR USE SILANO PEN
Before using this product, please read and follow these instructions carefully.
1. Indication Range
The Silano Pen Bonding system allows preparation of a chemical-micromechanical bond between acrylate-bases, light-curing or autopolymerizing resins and dental alloys as well as ceramics (incl. aluminum oxide and zirconium oxide).
The Silano Pen is used for surface pretreatment during the fabrication, repair, or processing of crowns, Maryland bridges, brackets, CoCr frameworks, attachments, inlays, onlays, veneers and others.
Additionally, the Silano Pen Bonding system is suitable for the following types of dental work:
" Acrylic veneering of metal framework
" Repair of acrylic veneers
" Repair of ceramic supply with acrylic veneering materials
" Repair of denture resins
" Conditioning of surfaces of adhesion joints
" Bonding of acrylic teeth with denture resins
" Thermal fine disinfecting and fine cleaning of surfaces
2. Features and Properties
The creation of highly stable and durable bonding between metal/ceramic and acrylic is based on the combination of a special gas mixture with a bonding liquid. The special gas mixture is processed with the firing device Silano Pen. Short firing with the Silano Pen results in fine cleaning and, simultaneously, silicate formation and activation of the surface to be processed. The ensuing application of the bonding agent optimizes the bond between the resulting silicate layer and the acrylic structure
3. Processing
3.1 Acrylic veneering of metal frameworks with light-curing, acrylate-based resins
3.1.1 Sandblasting
The surface to be coated is sandblasted with AI2O3 (disposable abrasive material: grain size 110 to 150 µm) at a pressure of 3 to 4 bar and then cleaned with water- and oil-free compressed air.
3.1.2 Silano Pen
The metal framework is evenly heated with the flame for 5 seconds per cm2 (see 6.1).
3.1.3 Applying the Bonding Agent
Once the fired surface has cooled down (below 50º C), the Bonding Agent is applied in accordance with the manufacturer's instructions (see 6.2) and allowed to dry at air for approximately 3 minutes.
3.1.4 Application of Opaque & Dentin
Apply and cure opaque and dentin in accordance with the manufacturer's instructions.
3.2 Repair of Acrylic and Ceramic Work (also Denture Resins)
3.2.1 Sandblasting
In order to prepare the object for new structuring, the repair surface is sandblasted with AI2O3 (disposable abrasive material: grain size 110 to 150 µm) at a pressure of 3 to 4 bar and cleaned up with water- and oil-free compressed air.
3.2.2. Silano Pen
Repair surface is evenly heated with the flame.
Processing times: Metal framework: approx. 5 sec/cm2
Ceramic: approx. 5 sec/cm2
Resin: approx. 2 sec/cm2
3.2.3 Applying the Bonding Agent
Once the fired surface has cooled down (below 50º C), the Bonding Agent is applied in accordance with the manufacturer's instructions (see 6.2) and allowed to dry at air for approximately 3 minutes.
3.2.4 Application of Opaque & Dentin
According to the requirements, opaque, dentin, or denture resin are applied and cured in accordance with the manufacturer's instructions.
3.3 Further possible applications
Application Processing Time Bonding Agent
Silano Pen
Integration of acrylic Acrylic tooth
teeth in denture resin approx. 2 sec/cm2 Yes
Ceramic tooth
Approx. 5 sec/cm2 Yes
Conditioning of Patrix and matrix
adhesive joints 5 seconds each Yes
Fine cleaning and Acrylic No
fine disinfecting of 2 x 2 sec/cm2
surfaces and (with break)
instruments
4. Operating the Silano Pen
When delivered, the Silano Pen is ready for operation.
Move the sliding switch (2) of the Silano Pen to"ON" until you can hear that the gas mixture escapes. By pressing in the spherical switch (5) at the opposite end of the flame outlet nozzle, the gas mixture is ignited.
A "pale-blue to violet" flame can be seen. The size of the flame is adjusted with the gas flow controller (3) (+/-). The supply of gas is interrupted by sliding back the sliding switch (2). Operating temperature of the Silano Pen: 15º to 25º C (also applies to filling).
5. Cleaning, filling and maintenance of the Silano Pen
5.1 Cleaning
The flame outlet nozzle (1) is cleaned with the small cleaning brush each time before the Silano Pen is filled. For this purpose, clean the nozzle with the brush for 30 seconds and push the bristles into the nozzle holes. Clean the nozzle area thoroughly with oil-free compressed air (2 to 4 bar) and remove loose particles in the nozzle openings.
5.2 Refilling with the enclosed cartridge
When refilling the Silano Pen, the refill cartridge and the pen must be at room temperature (15º to 25º C). Prior to filling with the refill cartridge, the flame outlet nozzle must be cleaned as described under section 5.1. Just before filling, the refill valve (4) is shortly pressed in several times using the shaft end of the brush to ensure that the pen is completely filled with gas. Shake the cartridge well and plug it into the refill valve of the Silano Pen (upside down). After the cartridge has been pressed into the filling inlet, the gas mixture flows into the Silano Pen. The filling time is 10 seconds and should not be exceeded.
5.3 Refilling with additional (max. number: 4) cartridges
Prior to using a new, closed cartridge, the sliding switch of the emptied pen must be moved to "ON" for at least 30 minutes to drain the gas tank completely. For this purpose, the Silano Pen is placed under an exhaust system or at an adequately ventilated area. Then the pen is filled as described under item 5.2.
5.4 Checking the flame size
The length of the inner, clearly visible flame cone (7) should be approximately 1.5 cm. at room temperature and maximum position of the gas flow controller. In case the flame length is more than 2 cm. Perfect-firing results can no longer be ensured.
Please note: The cartridge in the set allows to prepare approximately 2000 veneer units. The period of usage of the Silano Pen ends after a total number of 5 gas cartridges (maximum) have been filled into the pen. According to our current knowledge, the functional reliability of the pen is no longer ensured if the indicated period of usage is exceeded. Therefore, then pen must not be used after this period has expired.
6. Handling and processing
6.1 Silano Pen
The surface is heated with the "pale-blue" flame zone (6) of the pen (Fig. 2). The flame is continuously moved forward and backward across the activation surface so that uniform treatment of the entire surface is achieved. The preparation of the surface to be activated and the relevant processing times are described under item 3. The bonding agent is applied immediately after the heated/fire areas have cooled down below 50º C.
Please note: Insufficient distance or excessive distance between the flame and the surface to be treated results in a deterioration of the activation result. Contamination (fingers) of the treated surfaces will affect bonding of the subsequent layers. The entire activation process, starting with sandblasting (see item 3 - Processing), must be repeated in case of contamination.
6.2 Bonding Agent
Add the required quantity of bonding agent into the clean plastic cup. Take out the bonding agent using a disposable brush and apply thinly onto the cooled areas without the formation of puddles. Let the layer air dry for approximately 3 minutes and continue processing within 4 hours.
Please note: Excess quantity of bonding agent must not be refilled into the bottle. The bottle must be closed immediately after each use. Bonding agent solution must only be added into the clean plastic cup (wipe out carefully using paper towels, ethanol). Solution that has been added into the cup can be used within a period of up to 5 minutes. Contamination (fingers) of the treated surfaces will affect bonding of the subsequent layers; therefore, processing from sandblasting to the application of the opaque must be carried out without interruptions.
7. Safety Information and Hazard Warnings
7.1 Refill Cartridge and Silano Pen
" Highly flammable
" Store in cool place
" Injurious to health when inhaled
" Store container in a well ventilated place
" Keep away from ignition sources
" No smoking
" Protect against electrostatic charging
" Use product only in well ventilated areas
" Container is under pressure
" Do not expose to direct sunlight and temperatures above 50º C (e g incandescent lamps)
" Do not force containers open or burn them even after using
7.2 Agent
" Readily flammable
" Store in a cool place
" Injurious to health when inhaled
" Use product in a well ventilated area
" Store container well sealed in a well ventilated area
" Container must always be closed after each use
7.3 Storage Information
In the closed original packing, the shelf life of the refill cartridge is 12 months; it can be stored for 6 months in the open original packing. The maximum storage temperature is 15º C. Store Bonding Agent in a dark place. The indicated shelf life starts with the delivery date. The material must not be used any longer after the shelf life has expired. Direct sunlight must be avoided. Keep out of children's reach
8. Other information
The information contained in these instructions for use is always updated according to the latest knowledge and experience. Therefore, we recommend that you read these instructions again before using a new package. These instructions refer to Silano Pen, Item #320 004 70.
Bredent Casting Technique
Bredent Casting Technique According to Sabath
“A dental technician’s manual for producing precise fitting, homogenous and biocompatible dental castings”
The Bredent Casting Technique (According to Sabath) is an instructional user manual with simplified, reliable scientific data and experience in the dental casting process. The main purpose of the book is to provide practical knowledge for the dental technician rather than scientific or metallurgical formulas and processes. It is 230 page book assembled in a loose-leaf, hard-backed, ring binder style with 6 chapters.
Book Table of Content
Ch. 1: Investment Compounds - composition of investments and application ranges, processing information, wax movement and thermal wax tension, pressure investing, comparison of ring flasks systems and investing.
Ch. 2: Preheating (Burn-Out) - Linear preheating, Kiln types and their effects on investment ring molds, rapid fire-preheating techniques and practice-related case studies about preheating and castings fit results.
Ch. 3: Casting - Materials, alloy melting (flame, induction, resistance, electric arc), comparison of casting methods and their results.
Ch. 4: Cast-Port supply (Sprueing) – Direct and indirect sprueing techniques and inflow of metal.
Ch. 5: Bredent Casting Technique According to Sabath.
Ch 6: Refractory model casting techniques - Choosing proper sprues and attaching pressure equalization channels.
Book Preface by Peter Brehm, CEO (Bredent Germany)
Dentistry at large, and in particular, if it is performed while assuming the responsibility of harming the patient as little as possible by the jointly determined, necessary therapeutic measures, always depends on an appropriately geared dental technology for its implementation.
For this reason, bredent aim for the goal to offer both dentist and dental technician a closed system, which conveys optimal security and trust in all materials for the patient. Comprehensive system solutions offer a symbiosis of matching materials and devices, which minimizes the expenditure of human labor and increase precision, so that any working process can be organized in a more efficient and economic way. For the dentist, it is important to know that the quality of his work depends directly on the quality his dental technician delivers. And the dental technician in turn depends on the excellent quality of the materials made available to him.
As the human being develops, he places higher and higher demands on the quality of life. Right from the start, he learned from natural circumstances, influenced and changed them. He recognized chemophysical processes and developed techniques, which enabled him to create materials that are not found at all in nature. And ever since the scanning electron microscope was invented, he is able to analyze and refine most of these chemophysical processes as well.
Active, scientific work - regardless of which type - is subject to a continuously repeating cycle. Acquired knowledge is utilized, advanced, realized and analyzed. Moreover, the positive symptoms resulting from this etiology should be integrable into the repetitive cycle. Solutions are developed to realize knowledge. And those who advance will also meet success.
The more often each cycle is passed, the more knowledge we accumulate by new cognitions. The very same applies to the Bredent Casting Technique (according to Sabath).
The many years of dealing with the matter - in theory as well as in practice - can be evaluated and realized. Therefore, this book will give you information of how the consistent refinement of numerous options can realize your strive for perfection in casting technology.
I hope this book will help all readers and users to meet their individually desired goals.
Sincerely yours,
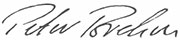
Peter Brehm, CEO
Bredent Germany
Bredent Casting Technique according to Andreas Sabath
Casting is not an invention made in modern times, but human being adopted this technique from nature. A volcano, called fire spitting mountain in the early times, erupted magma and gasses from the depth of the earth. This liquid lava broke its way into the valley through flow channels. The lava surface solidified and incrusted, and thus created bizarre outlines and formations. Lava that had entered certain terrains molded these shapes, and that way human beings recognized early that materials could be set in moulds.
The outer walls of the lava cooled down and solidified. Flow ducts, which maintained the heat within their centre, developed, and enabled the lava to flow steadily and to cover great distances within these channels. And after the human being gained control of the fire and learned to take advantage of it for himself, the Bronze Age and the Iron Age had begun.
The human being had learned to liquefy materials by fire, cast them in moulds, or turn them into different shapes by heating them with fire. He learned from nature first, and later on, he gained from it.
The half-life of knowledge got shorter and shorter. With the use of energies and the transmission of forces, technologies were more and more refined. Once mankind started to commit the knowledge in their minds to paper, progression - in the sense of improvement and advancement - became unstoppable. New insights lead to ever-growing new developments. And thus, the cycle proceeds towards new knowledge and advances our development.
We can, however, occupy ourselves with all developments and learn from them. Thus, each of us is influenced by others, and influences others in turn. A Everything that made an impact on us in the past will turn up again in various ways. Active scientific involvement - regardless of the development or advancement of knowledge - is subject to a continuously repeating cycle.
- We start the cycle by using acquired knowledge.
- We refine the acquired knowledge mentally and search for options.
- We attempt to realize our thoughts and insights.
- We examine the results of our attempts and analyze them.
- We recognize symptoms, both positive and negative ones.
- We search for causes that explain the positive symptoms, so that our results will become reproducible, and for solutions to the negative symptoms through new ideas.
- We develop solutions to realize these ideas.
- We realize the ideas and thus acquire new knowledge, which we take into consideration again and start the cycle at point A anew.
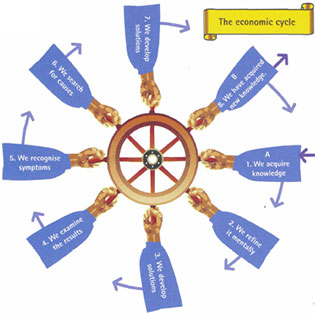
Only those problems of this cycle, which were solved by gaining new knowledge and thus broadened our knowledge and our insights without breaking the continuous cycle of collecting scientific knowledge, advance us in our development.
We should not regard this development as a burden, but as a chance. Only those who continuously advance will benefit from this in their professional life and will enjoy their work.
Science is not about teaching the truth, but represents result and sum of what we do repeatedly. The more often we pass or go through the cycle, the more knowledge we gather by experience. The same applies to the Casting Technique according to Sabath. The many years of dealing with this subject, in theory and practice, from own experience and from the knowledge of others, are evaluated and processed here.
The subject of casting also includes the working processes for fabricating moulds and the auxiliary materials required for this, and the chemophysical processes during melting, casting and the resolidification of materials. Based on this experience, the following chapters describe the various casting methods and cast port systems as well as their functioning.
In the descriptions of the processing and casting techniques, we frequently encounter developments, which were incorporated based on scientific research.
This book is designed as a handbook for the dental technician. For this reason, any scientific or metallurgic aspects as well as any chemical formula were deliberately omitted. It is strictly focused on the essential aspects that must be available to the dental technician in order to produce reproducible, homogeneous, and patient-compatible results. These are the standards by which the quality of dental prostheses is measured.
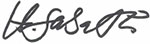
Andreas Sabath